Collaborative Product Data Management: The Ultimate Guide (2025)
In today's hypercompetitive manufacturing landscape, efficient collaboration around product data is no longer optional—it's essential for survival. As products grow more complex and teams become increasingly distributed across the globe, the need for robust collaborative product data management (PDM) systems has never been more critical.
This comprehensive guide explores how modern collaborative PDM solutions are transforming how engineering teams work together, streamlining workflows, and accelerating time-to-market in ways that were unimaginable just a few years ago.
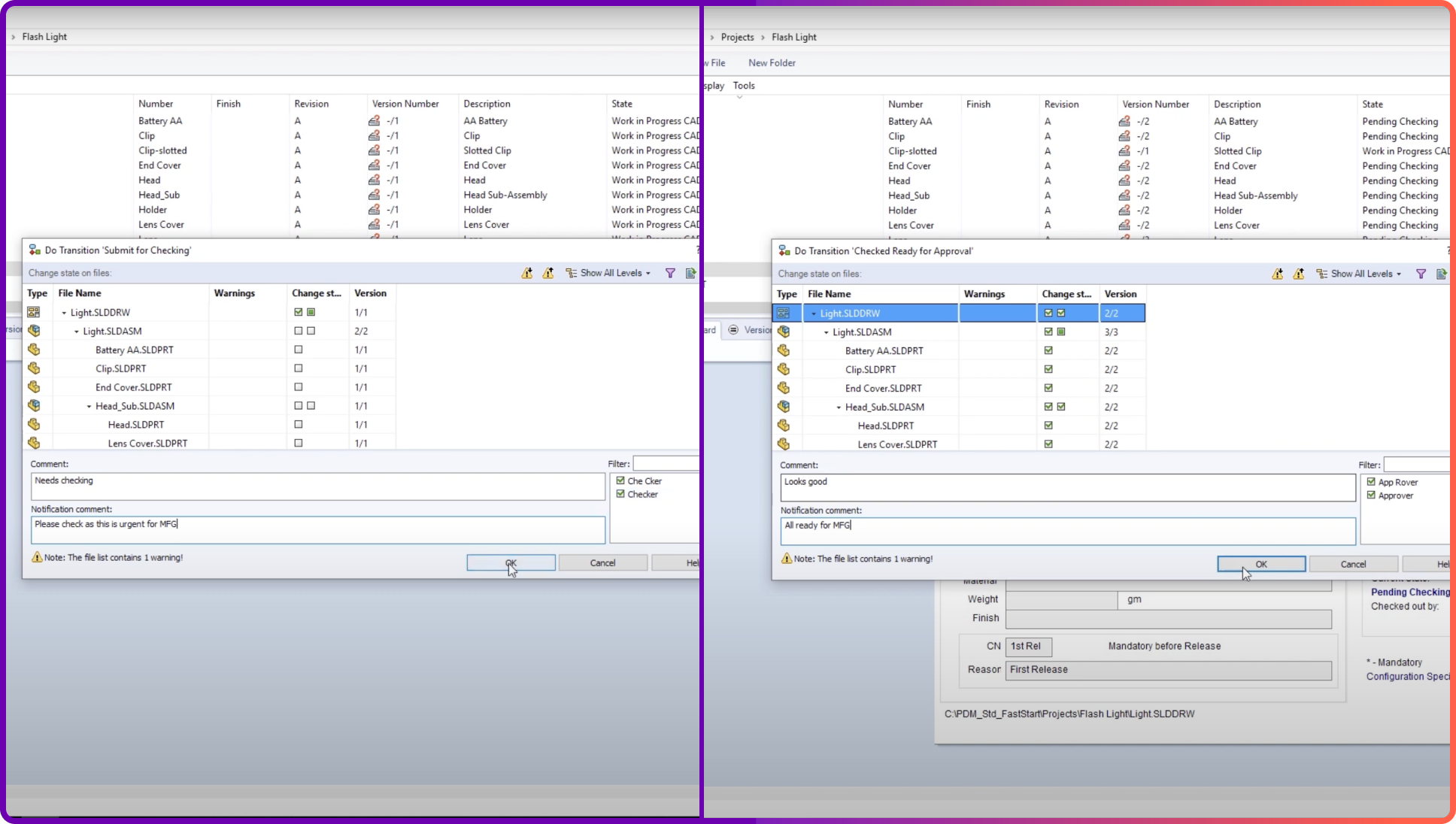
Key Takeaways:
- Collaborative PDM systems reduce development time by up to 30% through improved team coordination
- Cloud-based PDM enables real-time collaboration across global teams regardless of location
- Integration with CAD tools and enterprise systems creates a unified product development ecosystem
- Automated workflows dramatically reduce manual errors and ensure compliance
- Enhanced security features protect your valuable intellectual property while enabling collaboration
What Is Collaborative Product Data Management?
Collaborative Product Data Management (PDM) is a systematic approach to managing and controlling product-related information throughout its entire lifecycle. Unlike traditional PDM systems that focus primarily on file storage, collaborative PDM emphasizes streamlined information sharing, cross-functional teamwork, and concurrent engineering processes.
At its core, collaborative PDM creates a centralized, secure repository for all product data while providing tools for version control, change management, and role-based access. The collaborative aspect extends these capabilities through features designed specifically to enhance communication and coordination between team members, departments, and even external partners.
The Business Case for Collaborative PDM
According to a McKinsey report, organizations implementing collaborative product management solutions report up to 25% reduction in product development cycles and a 30% decrease in engineering change orders. These remarkable improvements stem from multiple factors:
Accelerated Time-to-Market
By enabling concurrent engineering processes where multiple team members can work simultaneously on different aspects of the same project, collaborative PDM significantly compresses development timelines. The traditional sequential approach gives way to parallel workflows, removing bottlenecks and idle time from the product development cycle.
Enhanced Quality and Fewer Errors
One of the most costly challenges in product development is rework due to errors or miscommunication. Collaborative PDM systems dramatically reduce these issues through:
- Controlled access to the latest version of files, eliminating work on outdated designs
- Structured approval processes ensuring proper review at each stage
- Centralized communication that keeps everyone informed of changes
- Automated validation checking that catches potential issues early
Improved Cross-Functional Collaboration
Modern product development requires input from multiple departments - engineering, manufacturing, marketing, purchasing, and quality assurance. Collaborative PDM breaks down information silos between these functions by:
- Creating a single source of truth for product information
- Providing role-appropriate views of complex data
- Enabling contextual discussions around specific components or assemblies
- Facilitating early involvement of downstream departments
This improved collaboration leads to better product decisions and fewer late-stage design changes, which are typically 5-10 times more expensive than changes made early in the development process.
"The companies that excel at product development don't just have better technology; they have better processes for collaboration across disciplines and departments."
— Harvard Business Review
Core Components of Effective Collaborative PDM Systems
An effective collaborative PDM solution combines several key capabilities to create a seamless environment for product development teams. Let's explore the essential components:
Centralized Data Repository
The foundation of any PDM system is a secure, centralized database that stores all product-related files and information. For collaborative systems, this repository needs to support:
- Multi-format data storage (CAD files, documents, specifications, test results)
- Robust metadata management for efficient searching and filtering
- Granular access controls based on roles and responsibilities
- Scalability to handle growing data volumes without performance degradation
Version Control and Change Management
Effective collaboration requires complete visibility into file history and changes. Advanced PDM workflows provide:
- Automatic version tracking with detailed change logs
- Check-in/check-out mechanisms to prevent conflicting changes
- Structured change request and approval processes
- Complete audit trails for regulatory compliance
Real-Time Collaboration Tools
Beyond basic file management, collaborative PDM systems include features specifically designed to facilitate teamwork:
- Embedded discussion threads linked to specific components or assemblies
- Visual markup and annotation capabilities
- Notification systems that alert team members to relevant changes
- Task management and assignment functionality
- Virtual design review sessions with multi-user participation
Workflow Automation
Automated workflows are a cornerstone of efficient collaboration, ensuring that processes follow established protocols and nothing falls through the cracks. Key capabilities include:
- Configurable approval sequences based on company standards
- Automatic routing of documents to appropriate stakeholders
- Status tracking and bottleneck identification
- Escalation procedures for delayed approvals
- Integration with email and messaging platforms for notifications
To learn more about implementing effective PDM workflows, check out our detailed guide on PDM workflow optimization.
Integration Capabilities
No PDM system exists in isolation. The ability to connect with other enterprise systems is crucial for collaborative environments:
- Seamless CAD integration (SOLIDWORKS, Autodesk, Siemens NX, etc.)
- ERP connectivity for BOM management and manufacturing planning
- PLM integration for complete lifecycle visibility
- Project management tool connections
- Authentication systems (Active Directory, SSO)
For SOLIDWORKS users, our guide on SOLIDWORKS PDM system requirements and installation provides valuable insights into integration considerations.
Implementing Collaborative PDM: Best Practices
Assess Your Organization's Readiness
Before selecting a PDM solution, evaluate your organization's current processes and collaboration maturity:
- Document existing workflows and identify pain points
- Assess team members' digital collaboration skills
- Review IT infrastructure capabilities (network, security, etc.)
- Identify integration requirements with existing systems
Develop a Phased Implementation Strategy
Rather than attempting a "big bang" implementation, consider a phased approach:
- Start with a pilot project involving a specific team or product line
- Implement core functionality first (repository, version control)
- Gradually add advanced features as users become comfortable
- Expand to additional departments based on lessons learned
Implementation Timeline Example:
- Months 1-2: System setup and configuration
- Months 2-3: Data migration and pilot with engineering team
- Months 4-5: Expansion to manufacturing and quality departments
- Months 6-8: Integration with ERP and other enterprise systems
- Months 9-12: Full deployment and process optimization
Provide Comprehensive Training
User adoption is critical to PDM success. Develop a robust training program that includes:
- Role-specific training modules tailored to different user types
- Hands-on workshops for practical experience
- Documentation and quick reference guides
- Designated "super users" who can provide peer support
- Ongoing training for new features and refresher sessions
Standardize Processes and Naming Conventions
Effective collaboration requires consistent approaches across the organization:
- Establish standardized file naming conventions
- Define metadata requirements for different document types
- Create templates for common documents and deliverables
- Document workflow procedures for key processes
For detailed guidance on standardizing file structures, our article on SOLIDWORKS Copy Tree functionality provides valuable insights into maintaining organized file hierarchies.
Cloud-Based vs. On-Premises Collaborative PDM
One of the most significant decisions when implementing a collaborative PDM system is whether to deploy in the cloud or on-premises. Each approach has distinct advantages and considerations:
Cloud-Based PDM Advantages
- Global Accessibility: Team members can access data from anywhere with an internet connection
- Reduced IT Overhead: Provider handles maintenance, updates, and security patches
- Scalability: Easy to add users and storage capacity as needs grow
- Subscription Model: Lower initial investment with predictable ongoing costs
- Continuous Updates: Automatic access to the latest features
On-Premises PDM Advantages
- Complete Control: Full administrative authority over system configuration and security
- Network Performance: Better performance for large files in local environments
- Data Sovereignty: Easier compliance with regulations requiring local data storage
- Customization: More extensive options for tailoring to specific requirements
- One-Time Licensing: Potentially lower long-term costs for stable environments
Hybrid Approaches
Many organizations are adopting hybrid approaches that combine elements of both deployment models:
- Core PDM functionality on-premises with cloud-based collaboration tools
- Local storage for large CAD files with cloud-based management interfaces
- Tiered access where internal teams use on-premises systems while external partners access cloud portals
Security Considerations for Collaborative PDM
While collaboration is essential, protecting valuable intellectual property remains a top priority. Effective security in collaborative PDM balances accessibility with protection:
Access Control and Authentication
- Role-based permissions that limit access based on job responsibilities
- Multi-factor authentication for sensitive data or administrative functions
- Single sign-on integration with enterprise identity management
- IP-based access restrictions for highly sensitive information
Data Protection
- End-to-end encryption for data in transit and at rest
- Secure sharing mechanisms for external collaboration
- Digital rights management for controlling document usage
- Automated backup and disaster recovery procedures
Audit and Compliance
- Comprehensive audit trails for all system activities
- Regular security assessments and vulnerability testing
- Compliance monitoring for industry regulations (ITAR, GDPR, etc.)
- Processes for responding to potential security incidents
For engineering teams working in regulated industries, additional security measures may be necessary. Learn more about industry-specific requirements in our article on PDM in engineering.
Future Trends in Collaborative PDM
The collaborative PDM landscape continues to evolve rapidly, with several emerging trends poised to transform how teams work together:
AI-Enhanced Collaboration
Artificial intelligence is beginning to play a significant role in collaborative PDM systems:
- Predictive analytics that identify potential design issues before they become problems
- Intelligent search capabilities that understand context and relationships
- Automated classification and tagging of documents
- Natural language processing for improved search and retrieval
- Recommendation systems that suggest relevant resources to team members
Extended Reality (XR) Integration
Virtual, augmented, and mixed reality technologies are creating new possibilities for collaboration:
- Virtual design review sessions with immersive 3D visualization
- AR-assisted assembly and maintenance procedures
- Remote expert assistance through shared AR views
- VR-based training for complex product interactions
Digital Thread and Digital Twin Integration
The concept of maintaining continuous data connections throughout the product lifecycle is gaining traction:
- Complete traceability from requirements to in-service performance
- Real-time feedback from physical products to design teams
- Simulation-driven design validation using digital twins
- Predictive maintenance based on operational data
Ready to Transform Your Product Development Process?
Discover how implementing a collaborative PDM system can accelerate innovation, reduce costs, and improve product quality in your organization.
Contact our team of experts for a personalized assessment of your PDM needs.
FAQs
How does collaborative PDM differ from PLM?
While related, Product Data Management (PDM) and Product Lifecycle Management (PLM) serve different but complementary purposes:
- PDM focuses on managing design data, documents, and related information during the development phase
- PLM extends this management across the entire product lifecycle from concept through retirement
Collaborative PDM can be viewed as a component within a broader PLM strategy, often serving as the foundation upon which more comprehensive lifecycle management is built.
What types of organizations benefit most from collaborative PDM?
While businesses of all sizes can benefit from collaborative PDM, certain characteristics indicate an organization will see particularly significant returns:
- Companies with geographically distributed teams
- Organizations developing complex products with multiple subsystems
- Businesses with cross-functional development processes
- Enterprises working with external partners or suppliers
- Companies in highly regulated industries with strict documentation requirements
How can I measure the ROI of a collaborative PDM implementation?
Key metrics to evaluate PDM return on investment include:
- Reduction in product development cycle time
- Decrease in engineering change orders and rework
- Time saved searching for and retrieving information
- Reduction in duplicate work and redundant data creation
- Improvements in first-time-right manufacturing
- Reduction in compliance-related issues or delays
How do we maintain performance when working with large CAD files in a collaborative environment?
Performance optimization strategies include:
- Implementing lightweight visualization formats for remote viewing
- Utilizing selective download approaches that retrieve only needed components
- Employing data caching mechanisms for frequently accessed files
- Optimizing network infrastructure for large file transfers
- Considering hybrid deployment models with local storage for CAD data
How can we ensure successful adoption of a new collaborative PDM system?
Successful adoption strategies include:
- Involving end-users in the selection and implementation process
- Clearly communicating the benefits and value proposition
- Providing comprehensive, role-specific training
- Designating champions within each department
- Starting with high-value, visible use cases
- Measuring and sharing success stories
- Continuously gathering and acting on user feedback
Conclusion
The evolution of product data management from simple file storage to comprehensive collaborative environments represents one of the most significant advancements in modern engineering practice. As products grow more complex and development teams more distributed, the ability to work together effectively across distances and disciplines has become a critical competitive advantage.
By implementing robust collaborative PDM systems, organizations can not only accelerate their development processes but also improve product quality, reduce costs, and foster innovation through improved cross-functional communication. The future belongs to companies that can effectively harness the collective intelligence of their teams through technology-enabled collaboration.
For organizations ready to take the next step, the investment in collaborative PDM represents not just an IT decision but a strategic commitment to excellence in product development and customer satisfaction.