Model-Based Enterprise: Improvement or Waste?
Are traditional 2D workflows costing your company valuable time and resources due to lost or outdated data? Explore the Model-Based Enterprise (MBE) concept—a powerful solution promising dramatic efficiency gains, and discover whether its transformative benefits outweigh the challenges for your business.
Do you know that your employees lose about 7 hours a week because they work with wrong, old or lost data? This figure comes from latest research by OnShape.
Why does it happen?
This inefficiency is primarily due to traditional company practices involving multiple documentation stages and formats, which lead to issues in document management, quality control, and workforce coordination.
Document Mess - Companies rely on outdated paper or 2D documents like PDFs and CAD drawings, requiring frequent manual updates that are error-prone and time-consuming.
Errors and Data Loss - Outdated documents can result in non-compliant products, while data spread across platforms increases error risks and slows development.
Workforce Challenges - The absence of a centralized system complicates role flexibility and coordination among departments, leading to delays and miscommunication.
So, is there a solution?
.webp)
Of course, there is! The solution is MBE, or Model-Based Enterprise. It is a relatively new, yet well-proven concept.
According to Data Bridge Market Research, the global model based enterprise market which was USD 22.11 billion in 2023, is expected to reach USD 83.45 billion by 2031, and is expected to undergo a CAGR of 18.06% during the forecast period of 2024-2031
MBE (Model-Based Enterprise) uses a collaborative 3D environment across a company, enabling real-time teamwork in multidisciplinary engineering. It replaces traditional 2D drawings with 3D models, utilizing integrated CAD, CAE, and CAM tools connected through a digital thread, enhancing efficiency and accuracy while maintaining consistent information access throughout a product's lifecycle.
The method incorporates detailed annotations and PMI (Product and Manufacturing Information) in the models to improve product understanding and production planning. As scientific studies suggest, this allows to reduce the cycle time by up to 75% compared to traditional design processes. Yes, you got it right - by three quarters!
Where and by what industries is MBE used?
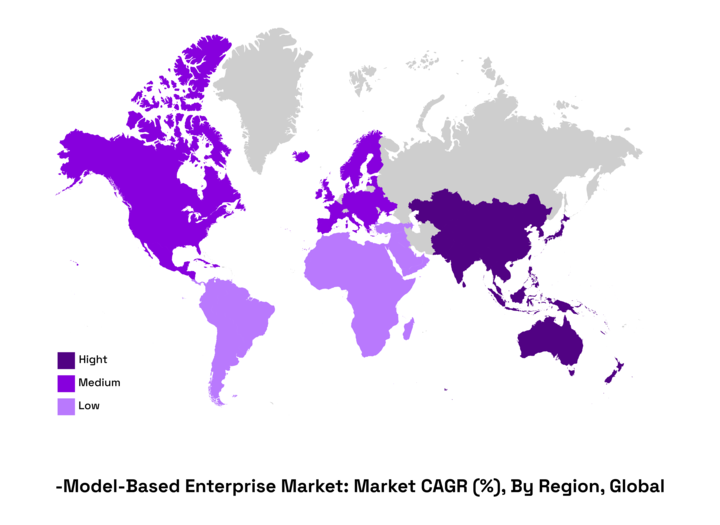
The leading position takes the North American market, but as MBE strategies continue to evolve, companies lagging in their adoption of these modern business management practices risk being outpaced.
Without embracing these trends, firms face potential replacement by more agile and innovative competitors from Asian economies, underscoring the critical need for continuous improvement and adaptation in today's global marketplace.
Among the industries, the automotive sector has been a pioneer in adopting model-based system technology, significantly boosting car sales in Europe as reported by ACEA, with a 17.8% increase in June from the previous year. The industry's embrace of modern and innovative approaches has established it as a leader in the MBE space.
Furthermore, sectors such as spacecraft, UAVs, and advanced manufacturing are also front runners in the MBE market, integrating cutting-edge technologies to enhance efficiency and performance. These industries are proving that sophisticated MBE solutions are essential for maintaining competitive edges.
Is MBE used by everyone?
No, not at all. Why? Adopting MBE means changing existing systems, which can be expensive and complicated. Employees might resist because they're used to doing things differently.
Also, implementing MBE costs money, while you need to buy new technology and train your employees. Small to Medium Businesses may spend tens to hundreds of thousands on software and training, while large enterprises might face costs from hundreds of thousands to millions due to complex software and compliance needs. Don’t forget about ongoing expenses for maintenance, updates, and training.
Last but not least - implementation takes time. A lot of time. Goal Definition and Planning, which means meeting with stakeholders to gather requirements and plan can take a few weeks or months. Creating the architecture and selecting software and design processes usually takes over a few weeks or months as well. Constructing or customizing MBE and integrating it with existing IT systems can approximately take several months to a year. Then testing - a few weeks to several months, depends on the size of your organization. And finally, deployment: Train users, implement the software and processes, and provide support for a few months on average.
Are there any solutions that are not so expensive, time consuming and difficult for employees?
Sure. Sibe is a platform that can be fully implemented in just a couple of weeks, offering a lower Total Cost of Ownership compared to larger market solutions. It seamlessly integrates into existing workflows without the need for replacements or major changes, maintaining the usual production processes.
Sibe excels in simplifying the transition from 3D CAD tools to the manufacturing floor, providing a fast track that bypasses the traditional complexities of turning 2D drawings into 3D models. Users access a straightforward, efficient website, enhancing productivity and reducing errors, making Sibe a practical choice for businesses aiming to streamline their manufacturing operations.
Plus, Sibe was designed with users in mind. It has an intuitive interface to reduce the learning curve and make the transition easier for employees, reducing resistance to new systems. Sibe has all the support and training materials you need to make sure it's used successfully.
In terms of price, Sibe is a budget-friendly option compared to more expensive, complex MBE solutions. It's much cheaper, so it's accessible for small and medium-sized businesses without sacrificing functionality. Its flexible design means businesses can expand the system as they grow and adapt to new requirements, without having to completely overhaul it.
Sibe solves common problems like cost, complexity, and resistance from employees, so it's a great option for companies who want to reap the benefits of a model-based system without all the usual headaches.